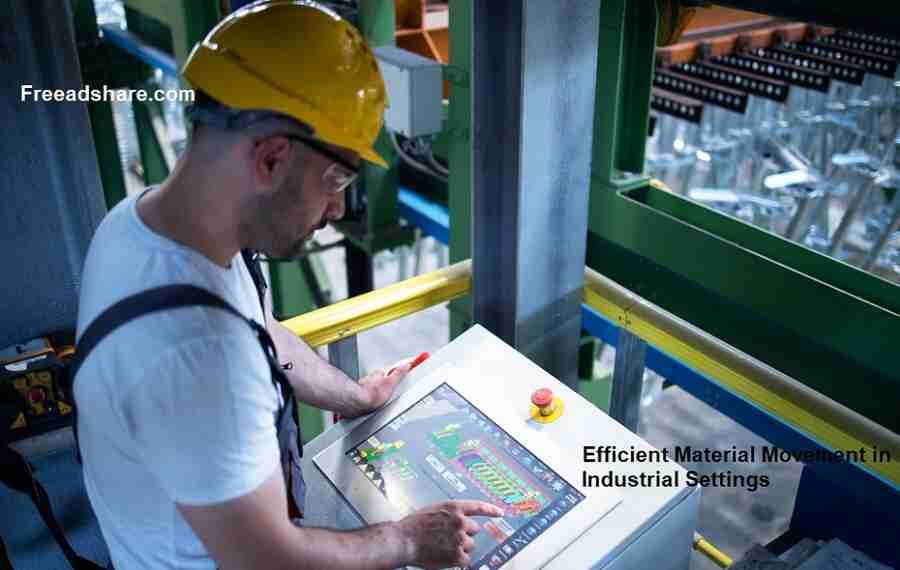
Why Smart Material Handling Matters
Efficient and safe material handling is the backbone of any industrial setting. When teams move items, equipment, or supplies, the methods and equipment chosen can have a lasting impact on operational flow and workplace health. Materials that are difficult to transport or require awkward lifting can easily cause delays or unnecessarily strain workers. Selecting components like rigid casters can be transformative. These casters provide steady, controlled motion, especially when transporting heavy items along predetermined routes or in environments where movement must be direct and stable.
Safety is more than a corporate buzzword—it is a fundamental necessity. According to the Occupational Safety and Health Administration guidance, material handling accidents remain among the top causes of warehouse injuries. Each incident leads to business disruptions, compensation costs, and—critically—diminished employee trust. When the right tools and mindsets are in place, the likelihood of these events drops substantially, creating safer, more productive environments for all involved.
Key Challenges in Industrial Material Movement
Material handling in industrial sites comes with unique pressures and constraints. Busy aisles, crowded loading zones, and high turnover between job sites make moving goods a complex puzzle. Congestion often slows down physical operations, leading to frustrating delays that can ripple through the day’s schedule. Teams are also frequently tasked with switching between tasks that may require drastically different equipment—sometimes with little notice—making flexibility a must.
- Fluctuating order volumes requiring agile responses
- Cumbersome storage that makes access time-consuming
- Manual tasks are prone to fatigue, strain, or repetitive injuries
- Inefficient layouts leading to double-handling or rework
These problems are rarely isolated, so any weak link in the movement process—outdated gear or traffic bottlenecks—can set off larger complications. Proactive planning, clear pathways, and equipment tailored to needs help keep operations running smoothly.
Modern Tools and Technologies for Efficiency
The last decade has seen dramatic shifts in the tools used to move materials. Traditional carts and fixed shelving have been replaced by modular, ergonomic alternatives that fit a range of environments and tasks. Adopting engineered wheels, flexible shelving, and intelligent conveyor systems means employers can move everything from small boxes to bulky pallets with less risk and greater speed.
The growing trend toward automation is reshaping the industry. As detailed in recent warehouse automation updates, the use of robotics has accelerated rapidly. Automated guided vehicles take over routine, repetitive deliveries, reducing workers’ wear and enabling them to focus on tasks that require problem-solving. These machines also offer precision, avoiding unnecessary stops or incorrect routing, which helps minimize injury and operational error. Investments in such technologies often have a fast, tangible payoff: organizations see fewer work-related injuries, better retention, and more streamlined turnarounds.
Creating a Culture of Safety
Establishing a strong safety culture is vital for every facility, large or small. When safety is embraced as part of daily routines rather than treated as an afterthought, it influences every aspect of industrial workflow. Scheduled training drills, visible procedures, and straightforward checklists keep safety in all team members’ minds. Many successful organizations implement safety walks and audits, where teams jointly identify hazards and discuss possible fixes.
- Continual equipment checks ensure reliability and safety for each shift
- Workshops and seminars, often led by staff, encourage peer learning and shared responsibility
- Safe storage and movement protocols reduce clutter and accidents
Empowering workers to voice concerns without fear of reprisal can be transformative. This collaborative approach guarantees that safety isn’t a hindrance, but rather the foundation for operational excellence.
Streamlining Workflow With Data
The integration of real-time data monitoring has revolutionized the pace and accuracy of facility operations. Advanced analytics platforms can record every step of a product’s journey through a warehouse, pinpointing precisely where and why bottlenecks occur. For example, if one section of a facility regularly experiences slowdowns, data might reveal that equipment wear or layout inefficiencies are to blame.
Equipping managers with dashboards and mobile tools allows them to schedule preventative maintenance, reroute goods quickly, or shift staffing to high-need areas. Companies that embrace data-informed strategies boost output and reduce unnecessary motion and associated wear on equipment. Furthermore, these insights are accessible to operations of all sizes—whether running global distribution hubs or local production lines—ensuring businesses compete on a level playing field.
Future Trends in Material Handling
Industrial material movement is on the brink of another transformation. Advances in smart technology allow equipment and software to “talk” seamlessly across the facility floor. Increased connectivity means sensors track temperatures, weight loads, and even vibration patterns, sending alerts when attention is needed. According to current industry projections, the warehouse automation market is expected to increase in value as more companies adopt these systems.
- AI-powered platforms will soon predict which assets are at risk of failing
- IoT-enabled tags help staff locate high-value or time-sensitive items instantly
- Flexible, modular robotics adjusts to changing workflow with little setup
- Human-machine partnerships empower teams to operate more safely and efficiently
As automation becomes more affordable, even small businesses can access high-quality solutions that allow for rapid scaling and permanent improvements to safety and productivity.
Training and Workforce Development
A cutting-edge warehouse is only as strong as the people who run it. Machines and software alone can’t replace the expertise of a well-trained, empowered workforce. Companies finding long-term success dedicate time to blended learning—layering online tutorials and simulations with real-world, hands-on instruction. Not only does this method cement important safety and equipment usage concepts, but it also adds confidence when staff adapt to new technologies.
- Role-based training ensures each employee knows their responsibilities and equipment specifics.
- Regular skill refreshers and mentorship programs strengthen knowledge retention.
- Team-building exercises centered on material movement foster collaboration
- Opportunities to provide feedback improve future training and morale
Facilities that invest in ongoing workforce development routinely report lower turnover, higher job satisfaction, and a record of accident-free operations.